Spot welding, a form of resistance welding, is a process used to join two or more metal sheets together by applying pressure and heat to the weld area. It involves the use of electrodes, typically made of copper, to apply an electric current to the metal pieces. This current generates heat due to the resistance in the materials, causing the metals to fuse together at a specific point or “spot.” The process is highly efficient for welding thin sheets of metal and is widely used in various industries due to its speed, reliability, and cost-effectiveness.
The evolution of spot welding machines has been marked by significant technological advancements. Early spot welders were large, stationary machines operated manually or by simple timers. As the demand for more precision and efficiency grew, technological improvements were made. The introduction of pneumatic and hydraulic systems allowed for better control over the welding pressure, enhancing the quality and consistency of the welds.
In the mid-20th century, the development of transistor technology and microprocessors brought about a new era in spot welding. Modern spot welders are equipped with sophisticated control systems that allow precise regulation of welding parameters such as current, force, and time. This has enabled the production of high-quality welds in a variety of metals and alloys, including those with high electrical conductivity or unique thermal properties.
Today, spot welding machines continue to evolve with the integration of advanced technologies such as robotics and computer numerical control (CNC), which offer greater automation, precision, and efficiency. These innovations have expanded the applications of spot welding in various industries, including aerospace, electronics, and construction, making it an indispensable tool in modern manufacturing processes.
This guide aims to serve as a comprehensive resource for understanding and navigating the complexities of spot welding machines. Our goal is to provide you with the essential knowledge and insights needed to make an informed decision when selecting a spot welding machine. We will navigate through the technical aspects, practical applications, and key considerations, ensuring that you are well-equipped with the information necessary to choose a machine that best suits your specific needs and applications. Whether you are a seasoned professional or new to the world of spot welding, this guide is your comprehensive companion, designed to demystify complexities and guide you towards a confident and informed choice in your spot welding endeavors.
In this guide:
Huge Savings on Spot Welders!
Check out our fantastic range of spot welding machines, electrodes and spares!
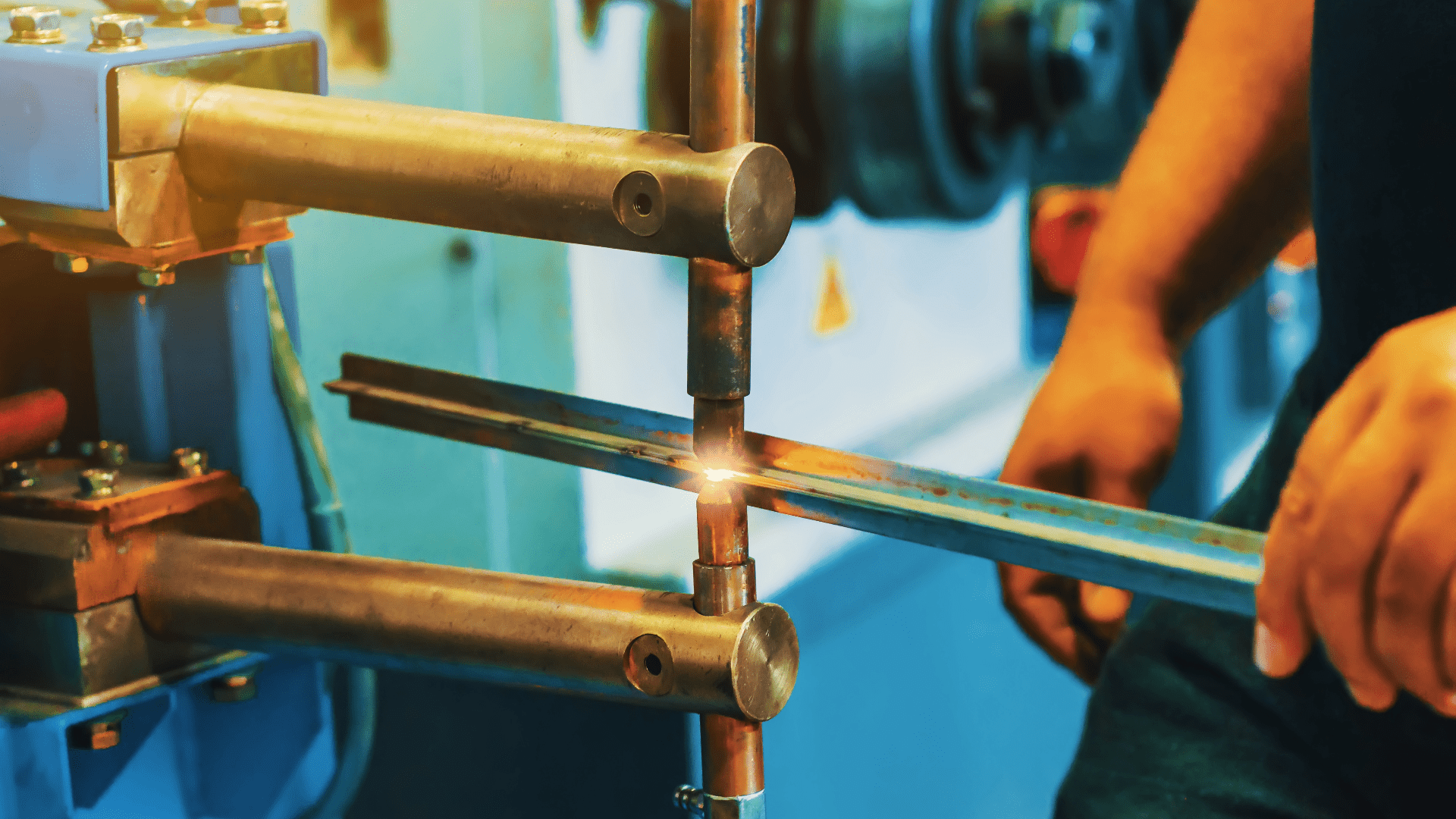
Types of Spot Welding Machines
Spot welding machines come in various designs and configurations, each suited to different applications and work environments. Understanding the types of spot welders available is crucial in selecting the right equipment for your specific needs. Here, we explore four primary types of spot welding machines: Portable, Bench, Pedestal, and Robotic Spot Welders.
Portable Spot Welders
- Description: Portable spot welders are compact and lightweight, making them ideal for on-site repairs or small workshops where space is limited. They are designed for ease of mobility and can be easily transported to different locations.
- Applications: These welders are commonly used in repair work, especially in automotive and construction industries, where mobility is essential. They are suitable for small-scale production or occasional welding tasks.
- Advantages: The main advantage of portable spot welders is their flexibility and ease of use in various locations. They are also relatively simple to operate, making them accessible to users with varying levels of welding experience.
Bench Spot Welders
- Description: Bench spot welders are designed to be mounted on workbenches, offering more stability and support for welding tasks. They are more powerful than portable models and provide greater control over the welding process.
- Applications: These are ideal for manufacturing environments where small to medium-sized components are welded. They are commonly used in electronic, jewelry, and dental industries.
- Advantages: Bench spot welders offer a balance between power and precision. Their stationary nature allows for more consistent welds and is suitable for repetitive tasks.
Pedestal Spot Welders
- Description: Pedestal spot welders are larger and more powerful than bench models. They stand on their own and are equipped with a pedestal, giving the operator a comfortable working height.
- Applications: These welders are used in industrial settings for welding larger and thicker materials. They are commonly found in automotive, aerospace, and heavy manufacturing industries.
- Advantages: Pedestal spot welders provide high precision and control, especially for larger workpieces. Their robust design is suitable for high-volume production and can handle a wide range of materials.
Robotic Spot Welders
- Description: Robotic spot welders represent the pinnacle of automation and precision in spot welding. These are highly advanced machines integrated with robotic arms, controlled by computer systems.
- Applications: They are predominantly used in large-scale manufacturing, such as automotive assembly lines, where high speed, consistency, and precision are paramount.
- Advantages: The primary advantage of robotic spot welders is their ability to perform complex and repetitive welding tasks with high efficiency and minimal human intervention. They offer unparalleled speed, accuracy, and consistency in welding.
Each type of spot welding machine offers unique benefits and is suited to specific applications. Understanding these differences is key to selecting the right spot welder for your specific requirements, ensuring optimal performance and efficiency in your welding projects.
Key Components of Spot Welding Machines
Spot welding machines consist of several critical components that work together to ensure efficient and effective welding. Understanding these components is essential for anyone looking to use or purchase a spot welding machine. This section covers the key components: Electrodes, Transformer, Controller, and Cooling System.
Electrodes
- Types and Materials: Electrodes in spot welding machines are typically made from copper or copper alloys due to their excellent electrical conductivity and heat resistance. There are various types of electrodes, including flat, dome, pointed, and offset, each designed for specific welding applications and material thicknesses.
- Maintenance: Regular maintenance of electrodes is crucial for consistent welding quality. This includes cleaning, reshaping, and occasionally replacing worn electrodes. Proper alignment and ensuring a clean contact surface are also essential for optimal performance.
Transformer
- Role: The transformer in a spot welding machine is responsible for converting the high-voltage, low-current power supply into a low-voltage, high-current output suitable for welding. This transformation is crucial for generating the heat needed to weld materials.
- Types: There are several types of transformers used in spot welding machines, including single-phase AC, three-phase AC, and DC transformers. The choice depends on the specific requirements of the welding application, such as the material type and thickness.
Controller
- Functionality: The controller is the brain of the spot welding machine. It regulates the welding current, time, and pressure, ensuring that each weld is consistent with the pre-set parameters. This is crucial for achieving uniform weld quality across multiple welds.
- Types: Controllers range from simple timer-based systems to sophisticated microprocessor-based controls. Advanced controllers offer features like programmable welding cycles, feedback systems, and integration with automation systems for precise control over the welding process.
Cooling System
- Importance: The cooling system in a spot welding machine is essential for dissipating the heat generated during the welding process. It prevents overheating of the electrodes and the transformer, which can lead to equipment damage and reduced weld quality.
- Types: Cooling systems can be air-cooled or water-cooled. Air-cooled systems are typically used in lower-duty applications, while water-cooled systems are preferred for high-duty cycles and industrial applications due to their superior cooling efficiency.
Each of these components plays a vital role in the operation of a spot welding machine. Understanding their functions and maintenance requirements is key to ensuring the longevity and efficiency of the equipment, as well as achieving high-quality welds in your projects.
Factors to Consider When Buying a Spot Welder
Selecting the right spot welder requires careful consideration of various factors to ensure that the equipment meets your specific needs. Here are key factors to consider:
Material Thickness and Type
The thickness and type of material are among the most critical factors in selecting a spot welder. This is because different materials and their thicknesses have unique electrical and thermal properties, which significantly influence the welding process. The effectiveness of a spot weld, in terms of strength and quality, is highly dependent on the welder’s ability to provide the appropriate amount of heat and pressure. Materials with high thermal conductivity require more energy to reach the necessary welding temperature, while those with high electrical resistance generate more heat at the weld point.
Considerations:
- Range of Material Thickness: The spot welder you choose should be capable of handling the range of material thicknesses you plan to work with. Thinner materials require less welding current and pressure to avoid burn-through, while thicker materials need higher current and pressure to ensure proper weld penetration.
- Material Type: Different materials react differently to spot welding. For instance, aluminum has high thermal conductivity and requires a welder with higher power output compared to steel. Stainless steel, known for its higher electrical resistance, also demands a welder that can deliver higher energy levels.
- Welder Specifications: Check the welder’s specifications to ensure it matches the requirements of your materials. Look for the maximum and minimum material thicknesses the welder can handle and its adaptability to different types of metals.
- Weld Quality: The quality of the weld is paramount. Ensure that the welder can produce consistent, high-quality welds on the types of materials you’ll be working with. This is particularly important in applications where weld integrity is critical, such as in structural or load-bearing components.
- Adjustability: A welder with adjustable welding parameters (current, time, pressure) is beneficial. This allows for fine-tuning the welding process to accommodate various materials and thicknesses, ensuring optimal weld quality.
- Testing and Trials: If possible, test the welder on samples of the materials you intend to use. This hands-on trial can provide valuable insights into the welder’s capability and suitability for your specific applications.
By giving careful consideration to the material thickness and type, you can select a spot welder that not only meets your current needs but also offers the versatility to handle a variety of welding tasks, ensuring a valuable and long-term addition to your welding equipment.
Power Supply Requirements
The power requirements of spot welders are a critical aspect to consider, as they directly impact the machine’s performance and suitability for specific tasks. Spot welders are rated based on the electrical current they draw, typically measured in amperes (amps). This rating is not just a measure of the power consumption but also an indicator of the welder’s capability to generate the necessary heat for welding.
- Welder Power Rating: The power rating of a spot welder often determines the maximum thickness of metal it can effectively weld. Higher amperage welders can handle thicker materials, but they also consume more power.
- Matching Power Supply: It’s essential to ensure that your power supply can adequately support the welder’s requirements. An undersupplied welder may not reach the necessary welding temperatures, leading to weak or incomplete welds.
- Circuit Breaker Rating: Check the rating of the circuit breakers in your electrical system. The welder should be compatible with the breaker’s rating to prevent tripping during operation.
Electrical Infrastructure:
The existing electrical infrastructure of your workspace can greatly influence the type of spot welder you can effectively use. Not all electrical setups are created equal, and some welders may have specific requirements that need to be met.
- Voltage Requirements: Some industrial-grade spot welders may require a higher voltage supply, such as 240V or 480V, compared to standard 120V outlets. Ensure that your workspace’s electrical system can provide the necessary voltage.
- Three-Phase Power: High-powered welders, especially those used in industrial settings, may require three-phase power, which offers more consistent power delivery and efficiency for heavy-duty welding. This type of power is not available in all locations, particularly in residential areas or smaller workshops.
- Electrical Upgrades: In cases where your current electrical infrastructure does not meet the requirements of the desired spot welder, consider the feasibility and cost of electrical upgrades. This may include installing new circuits, upgrading existing ones, or even bringing in a three-phase power supply.
- Portable Generators: For locations without the necessary power infrastructure, portable generators might be a solution. However, ensure that the generator can provide stable and sufficient power for the welder’s needs.
By thoroughly understanding and evaluating the power supply requirements and the electrical infrastructure of your workspace, you can ensure that the spot welder you choose not only fits within your current setup but also operates efficiently and effectively, providing the desired welding outcomes.
Duty Cycle
The duty cycle is a critical specification in spot welding machines, indicating the duration a welder can operate at a specific output without the risk of overheating and needing a cool-down period. It is expressed as a percentage and is typically based on a 10-minute cycle. For example, a duty cycle of 60% means the welder can run continuously for 6 minutes at the specified output and then must cool down for the remaining 4 minutes.
Understanding Duty Cycle in Practical Terms:
- Heat Management: The duty cycle is essentially a measure of a welder’s ability to manage heat. Prolonged use at high outputs generates significant heat, which can damage the machine if not properly managed.
- Impact on Welding Operations: A higher duty cycle is particularly important in industrial settings where spot welding is continuous and production rates are high. A lower duty cycle means more frequent pauses in work to allow the machine to cool down, potentially affecting productivity.
Selection Criteria:
- Assessing Workload: When choosing a spot welder, consider the intensity and frequency of your welding tasks. For heavy, continuous welding operations, a high duty cycle is essential to maintain productivity and reduce downtime.
- Duty Cycle for Intensive Use: For industrial applications or workshops where welding is a constant activity, look for a welder with a duty cycle of 70% or higher. This will ensure that the welder can keep up with the demands of a busy work environment.
- Duty Cycle for Occasional Use: If the welder is intended for occasional use, such as for small repairs or hobby projects, a lower duty cycle (e.g., 20-50%) may be entirely adequate. These welders are typically more affordable and can handle the sporadic nature of the work without overheating.
- Balancing Cost and Efficiency: Higher duty cycle welders often come at a higher cost. Balance the need for a high duty cycle with your budget constraints. In some cases, investing in a higher duty cycle welder can be more cost-effective in the long run, especially if it means avoiding work stoppages and equipment damage.
Additional Considerations:
- Environmental Factors: The ambient temperature in your workspace can affect the duty cycle. Hotter environments may reduce the effective duty cycle of the welder.
- Cooling Systems: Welders with advanced cooling systems can often sustain higher duty cycles. Consider the efficiency of the cooling system when evaluating a welder’s duty cycle.
By understanding and considering the duty cycle in the context of your specific welding needs, you can select a spot welder that not only fits your operational requirements but also ensures longevity and reliability of the equipment under the conditions in which it will be used.
Control Systems and Automation
The control system of a spot welder is a key factor that determines the precision, ease of use, and versatility of the machine. Control systems in spot welders range from simple to highly sophisticated, catering to different levels of welding requirements and expertise.
- Manual Controls:
- Description: Manual control systems are the most basic form of controls found in spot welders. They require the operator to manually adjust the welding parameters such as time, current, and pressure.
- Suitability: Ideal for simpler applications where the welding conditions are relatively constant or where high precision is not critical. They are also a good choice for users who prefer hands-on control over the welding process.
- Semi-Automatic Controls:
- Description: These systems offer a mix of manual and automated controls. Operators can set certain parameters, and the machine controls others automatically.
- Benefits: They provide a balance between control and convenience, suitable for applications that require consistent quality but also need some level of manual intervention.
- Programmable Logic Controllers (PLCs):
- Description: PLCs represent a more advanced control system. They allow for the programming of multiple welding parameters, enabling precise control over the welding process.
- Advantages: PLCs are ideal for complex welding tasks that require high precision and repeatability. They can store multiple welding programs, making them suitable for applications that involve a variety of welding tasks.
- Computerized Numerical Control (CNC):
- Description: CNC systems are at the forefront of welding technology, offering the highest level of automation and precision. They are computer-controlled and can be programmed for complex welding patterns and sequences.
- Application: CNC systems are essential in high-volume production environments where precision and repeatability are paramount. They are commonly used in automotive and aerospace industries.
Automation Needs:
- Precision and Repeatability: Automated control systems are crucial in environments where precision and repeatability are key. They ensure that each weld is consistent with the last, which is vital in high-quality manufacturing processes.
- Volume of Production: In high-volume production settings, automated controls significantly enhance efficiency and productivity. They reduce the need for manual adjustments and allow for faster, more consistent welding cycles.
- Complexity of Welding Tasks: For complex welding tasks, especially those involving intricate patterns or multiple welding points, automated controls provide the necessary precision and control.
- Skill Level of Operators: Automated systems can compensate for varying skill levels among operators, ensuring consistent quality regardless of the operator’s expertise.
- Integration with Other Systems: In advanced manufacturing setups, spot welders with automated controls can be integrated with other systems, such as robotic arms or conveyor belts, for a fully automated production line.
Considering the control systems and automation needs is crucial in selecting a spot welder that not only meets your current requirements but also aligns with future growth and technological advancements in your welding processes.
Size and Portability
The physical size of the spot welder is an important consideration, especially in environments where space is at a premium. The dimensions of the welder should be compatible with the available workspace, not only for operational efficiency but also for safety and ease of use.
- Assessing Workspace Dimensions: Before selecting a spot welder, measure the available space in your workshop or facility. Consider not just the footprint of the welder but also the additional space needed for safe operation, including access for loading and unloading materials and maintenance activities.
- Storage Considerations: If the welder will not be used continuously, think about storage options. A compact welder is easier to store when not in use, especially in multi-purpose workspaces.
- Workbench Integration: For smaller or benchtop models, consider how the welder will integrate with existing workbenches or tables. Ensure that the work surface can support the weight and operational vibrations of the welder.
Portability: Portability is a key factor if the welder needs to be moved regularly, either within a single facility or to different locations. Portable welders offer flexibility but may have trade-offs in terms of power and capacity.
- Lightweight and Compact Models: For maximum portability, look for welders that are lightweight and have a compact design. These models are easier to move and set up, making them ideal for on-site repairs or small workshops.
- Mobility Features: Features like wheels or handles can significantly enhance the portability of a spot welder. Wheeled models are easier to move around, especially for heavier machines.
- Transportation Needs: Consider how the welder will be transported if it needs to be moved between different sites. Some portable welders are designed to be easily loaded into a vehicle, while others might require more specialized transportation methods.
- Power Source Considerations: For portable welders, consider the availability of a suitable power source at different locations. Battery-operated or generator-compatible models offer more flexibility in locations without convenient access to electrical outlets.
Balancing Size and Functionality:
- Trade-offs: Be aware that there may be trade-offs between the size/portability of a welder and its capabilities. Smaller, more portable models might not have the same power or features as larger, stationary units.
- Future Needs: Consider not only your current space and portability needs but also potential future changes in your workspace or operational requirements.
By carefully considering the size and portability of a spot welder in relation to your workspace constraints and mobility needs, you can select a machine that not only fits physically in your environment but also aligns with your operational workflow and flexibility requirements.
Common Features of Spot Welders
- Microprocessor Control: Advanced spot welders often incorporate microprocessor controls for precise regulation of the welding process. This technology ensures consistent weld quality and allows for fine-tuning of welding parameters.
- Pneumatic Operation: Pneumatic systems are commonly used in spot welders for efficient and effortless operation. This feature enhances the ease of use and can improve the speed of the welding process.
- Advanced Welding Features: Features such as pre-weld current settings, pulse functions, and constant current modes are available in higher-end models. These advanced options allow for greater control and adaptability in various welding situations.
- Energy Efficiency: Modern spot welders are designed with energy efficiency in mind, helping to reduce electricity consumption and operational costs.
- Cooling Systems: Water cooling systems are a standard feature in many spot welders. They help maintain optimal operating temperatures, prolonging the machine’s life and allowing for extended use without overheating.
- Safety and Ergonomics: Safety features like heat-resistant covers, emergency stop buttons, and thermal overload protection are commonly included. Ergonomic design and portability features, such as lightweight construction or wheels, are also considered for user convenience.
- Customization and Versatility: Spot welders often offer customizable options like interchangeable arms and electrodes to accommodate different welding requirements and workpiece sizes.
- Built-in Electronic Timers: Integrated electronic timers with adjustable cycle settings are a standard feature, allowing users to control the duration and intervals of the welding process accurately.
- Durable Construction: Durable materials and construction, such as robust electrode holders and high-grade insulation on transformers, are typical to ensure longevity and consistent performance.
- User-Friendly Interface: Clear and intuitive interfaces are a key feature, with displays and controls that allow easy adjustment of welding parameters and monitoring of the process.
- Compliance with Standards: Adherence to relevant safety and quality standards is a crucial aspect, providing assurance of the equipment’s reliability and safety.
These common features across various spot welders highlight the focus on precision, efficiency, safety, and user-friendliness in their design, catering to a wide range of applications from automotive bodywork to industrial fabrication.
Safety Features
Safety is paramount in any welding operation. Spot welders, with their high electrical currents and heat generation, come with inherent risks. Therefore, it’s crucial to consider the safety features of a spot welder to protect both the operator and the equipment. Here’s an expanded look at essential safety features and compliance standards:
Essential Features:
- Heat-Resistant Covers: Given the high temperatures involved in spot welding, heat-resistant covers are essential. They protect the operator from accidental burns and reduce the risk of fire hazards in the workplace.
- Emergency Stop Buttons: An easily accessible emergency stop button is a critical safety feature. It allows the operator to immediately shut down the machine in case of an emergency, preventing accidents and equipment damage.
- Thermal Overload Protection: This feature helps prevent the welder from overheating. It automatically shuts down the machine if it exceeds a certain temperature, protecting the internal components from heat damage and reducing the risk of fire.
- Insulation and Grounding: Proper insulation and grounding of the welder are crucial to prevent electrical shocks. Ensure that the welder has adequate insulation on all electrical components and is properly grounded.
- Safety Interlocks: Safety interlocks prevent the welder from operating under unsafe conditions, such as when the cover is open or if a safety guard is not in place.
- Fume Extraction: Some spot welders come with fume extraction systems or are compatible with external systems. This is important for maintaining air quality and reducing the inhalation of harmful fumes.
- Arc Flash Protection: In certain types of spot welding, there’s a risk of arc flash – a dangerous burst of energy from the weld point. Welders with arc flash protection help mitigate this risk.
Compliance:
- Industry Standards: Ensure that the spot welder complies with relevant industry standards and regulations. This may include standards set by organizations like the American Welding Society (AWS), Occupational Safety and Health Administration (OSHA), or specific electrical and machinery safety standards relevant to your region.
- Certifications: Look for certifications from recognized bodies that indicate the welder has been tested and meets specific safety criteria. Certifications might include CE marking in Europe, UL listing in the United States, or others depending on your location.
- Manufacturer’s Safety Record: Research the manufacturer’s safety record and reputation in the industry. Manufacturers with a strong commitment to safety are more likely to produce reliable and safe equipment.
- Training and Manuals: Ensure that the spot welder comes with comprehensive user manuals and safety guidelines. Proper training for operators on the safe use of the equipment is also crucial.
By prioritizing safety features and compliance with safety standards, you not only protect the operators and other personnel but also ensure the longevity and reliability of the spot welding equipment. This proactive approach to safety can also help in avoiding costly accidents and potential legal issues.
Using a Tool Balancer with a Spot Welder
A tool balancer is a device used to suspend and balance heavy tools, like spot welders, in a position that makes them easier and safer to manipulate. It is particularly useful in reducing operator fatigue, improving precision, and enhancing safety in repetitive welding tasks.
Benefits of Using a Tool Balancer with a Spot Welder:
- Reduced Operator Fatigue: By counterbalancing the weight of the spot welder, a tool balancer makes it easier for operators to maneuver the welder, especially during prolonged use.
- Increased Precision: Balancers allow for smoother and more controlled movement of the spot welder, leading to more precise placement and better quality welds.
- Enhanced Safety: Reduces the risk of strain injuries and accidents caused by handling heavy equipment, as the balancer supports the weight of the welder.
- Improved Productivity: Operators can work faster and more efficiently as the tool balancer minimizes the physical effort required to position and use the spot welder.
Choosing the Right Tool Balancer:
- Weight Capacity: Ensure the tool balancer can support the weight of your specific spot welder model. Overloading the balancer can lead to equipment failure and safety hazards.
- Range of Motion: Consider the required range of motion for your welding tasks. The balancer should allow for easy movement across the necessary work area.
- Mounting Options: Tool balancers can be mounted on overhead systems, workbenches, or mobile frames. Choose a mounting option that best fits your workspace and workflow.
- Adjustability: Look for balancers with adjustable tension settings, allowing you to fine-tune the balance based on the tool’s weight and operator preference.
Installation and Usage Tips:
- Secure Installation: Ensure the tool balancer is securely installed and regularly check its mountings and fittings for any signs of wear or loosening.
- Balancing the Tool: Adjust the balancer to perfectly counterbalance the weight of the spot welder, ensuring it remains in position when not actively being moved.
- Training: Train operators on how to properly use the tool balancer with the spot welder, emphasizing the importance of not exceeding the weight limit and how to adjust the tension.
- Regular Maintenance: Regularly inspect and maintain the tool balancer, checking for any signs of damage or wear, especially in the cables or springs.
Safety Considerations:
- Regular Inspections: Regularly inspect the tool balancer for any signs of wear, especially in high-stress components like cables and springs.
- Avoid Overextension: Teach operators to avoid overextending the balancer’s range, as this can lead to mechanical stress and potential failure.
- Emergency Procedures: Establish procedures for safely handling situations where the tool balancer might fail or when the spot welder becomes unbalanced.
Incorporating a tool balancer with a spot welder can significantly improve the ergonomics and efficiency of welding operations. By carefully selecting, installing, and maintaining the tool balancer, you can enhance the overall safety and productivity of your welding tasks.
By carefully evaluating these factors, you can choose a spot welder that not only meets your current requirements but also offers flexibility for future projects. This approach ensures a wise investment in equipment that will serve your welding needs effectively and safely over time.
Maintenance and Safety
Routine Maintenance Tips:
- Regular Inspection: Conduct regular inspections of the spot welder, focusing on the condition of electrodes, electrical cables, and connections. Look for signs of wear, damage, or loose connections.
- Cleaning: Keep the welder clean from dust, dirt, and welding debris. Accumulated debris can lead to overheating and electrical malfunctions.
- Electrode Maintenance: Check the electrodes regularly for wear and alignment. Misaligned or worn electrodes can result in poor weld quality. Replace or dress the electrodes as needed.
- Cooling System Check: For welders with a cooling system, regularly check for proper coolant levels and signs of leaks. Ensure the cooling system is functioning efficiently to prevent overheating.
- Lubrication: Lubricate moving parts as per the manufacturer’s guidelines to ensure smooth operation and prevent wear.
- Software Updates: For welders with digital controls or PLCs, keep the software updated to ensure optimal performance and access to new features or bug fixes.
Safety Precautions and Best Practices:
- Personal Protective Equipment (PPE): Always wear appropriate PPE, including welding gloves, eye protection, and fire-resistant clothing.
- Workspace Safety: Keep the welding area clean and free of flammable materials. Ensure good ventilation to avoid the accumulation of toxic fumes.
- Electrical Safety: Always turn off and unplug the welder before performing any maintenance. Follow lockout/tagout procedures as necessary.
- Training: Ensure all operators are properly trained in the safe use of the spot welder and are aware of the specific safety features of the equipment.
- Emergency Procedures: Familiarize yourself and your team with emergency procedures, including how to use the emergency stop button and first-aid measures for welding-related injuries.
Troubleshooting Common Issues:
- Weak Welds: If the welds are consistently weak, check the electrode pressure, heat settings, and the condition of the electrodes.
- Overheating: If the welder overheats frequently, check the duty cycle compliance, cooling system functionality, and ensure the welder is not overloaded.
- Electrical Problems: Issues like erratic welding performance or failure to start may indicate electrical problems. Inspect electrical connections, cables, and switches.
- Inconsistent Weld Quality: Variability in weld quality can be due to misaligned electrodes, incorrect settings, or fluctuations in power supply. Regular calibration and maintenance can help mitigate these issues.
- Noise or Vibration: Unusual noise or vibration during operation may indicate loose components or mechanical issues. Inspect and tighten any loose parts and check for signs of wear or damage.
Regular maintenance and adherence to safety practices are crucial for the efficient and safe operation of a spot welder. By proactively addressing maintenance needs and following best safety practices, you can ensure the longevity of the equipment and the safety of its operators.